Worked all summer on the daily composition series. Soon enough they became multi-day compositions as I inevitably began to do more designing and started to enlarge the parts. Enlarging required laminating multiple pieces of plywood and that takes extra work. My goal was still to maintain a freshness that came along with not really knowing where they were going until I got there. If your a creative maker you'll know what I mean.
I made a lot of them, a lot. Then I went even bigger, I needed to really push where I could go with the line weights of the edges and the relative volume of the forms. Juxtaposing thin and thick forms is really starting to add some excitement to the pieces. It also means more planning with the construction, but I love the engineering part; problem solving is the best part. The solutions are even better. I also did a curved plywood shape. Love it! Will do more soon but I have some additional construction design to master.
 |
Rim Fire, 52" tall, 2013, wood. Currently at the USM faculty show at Oddfellows Gallery in downtown Hattiesburg, until the closing of the Fall Art Walk on October, 16. |
 |
Cloud Atlas, 28" tall, wood, 2013, will be at the Train Depot Show, starting on the Fall Art Walk, in downtown Hattiesburg, October 16. |
Just a few days ago I started to work out the fabrication process for hollow forms. I really want to go bigger. Although the last two works are made to come apart as a whole I am reaching the limits of what some of the smaller scale materials will handle without permanent attachments. I can't ship big pieces like this, not without winning the lottery, so they need to be modular. Waste also comes into play; a quadruple thick lamination of 3/4" thick plywood is not only wasteful but also heavy and expensive!
Hollow forms have a huge advantage, once I master the
making part. So far they are coming out well. The first one, a true prototype, went together pretty fast and skinned really well. The second one is much better as I leaned a lot about what will make gluing the skin on faster and easier. They do go together pretty well, but perfecting the engineering for that part will have to wait until I have more shapes to work with.
 |
The shapes must be perfect copies of each other. |
 |
I winged it with the glue blocks, not knowing what I really needed. Turns out I needed blocks in strategic places for the air nailer and clamps to work well. |
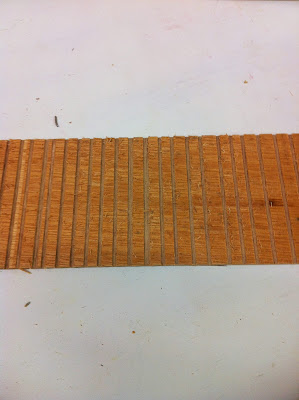 |
How to make bendy plywood. |
 |
Skin fits well. |
 |
Second one has much better glue blocks shaped to fit the corners. Still have to skin this one. |
 |
Two pieces slotting together. They fit very tight, maybe too much. |
Now to make some additional shapes, I need to master the technique so that I can make them fast and make many. I also need to work out thick to thin shapes. These are about 4" thick, I want to go much fatter.
More images soon!
Jen, these wooden works would make GREAT BIG STEEL pieces on city streets...I love the kinetic pieces..wish Athens 'Cultural Arts Committee' had just a modicum of VISION..you would look great here.. My best, kid.
ReplyDelete